Re-roofing your home or commercial building with metal is a great way to protect it. When done correctly, a metal roof is durable and can increase your property’s value.
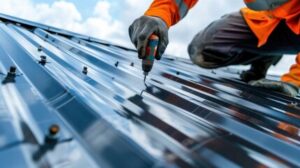
Most installation prices are quoted by the roofing square, which equals 100 square feet of surface area. Other factors include the size of the roof, roof pitch, and materials choices. Contact Metal Roofing Installation Columbus GA for professional help.
When a new metal roof is installed, the old materials need to be removed. This can be a big job and should be done carefully. Once the old materials are removed, a clean and stable base is left to work with. This is the foundation for your new roof and will need to be free of rot, moisture, or damage from existing shingles. Once the sheathing is clean, it can be prepared for the new roof by laying an underlayment.
This layer is essential to ensure the longevity of your new metal roof. It protects the sheathing and helps prevent water infiltration, which can cause rust and other issues that may impact the structural integrity of your building. There are many different types of underlayments available for metal roofing, so choose one that is suitable for your project.
Once the underlayment is in place, you can begin adding your panels. It’s important that the panels are secured and overlapped, which will help with water drainage and provide a clean, seamless appearance. You should also be sure to seal critical areas, such as valleys, flashing, and roof edges, to keep moisture from seeping into your home or business.
To secure the panels, you will need to use screws or rivets spaced evenly along each rib or ridge. If you are using exposed fastener panels, be sure to use stainless steel screws with rubber washers to avoid leaks.
It’s also a good idea to use galvalume or galvanized nails and screws, as these are less likely to rust over time. Galvalume is a metal coating that starts out as carbon steel and is hot-dipped with aluminum and zinc alloys to achieve a corrosion-resistant finish.
If your roof has a lot of exposed fasteners, it’s important to clean the area around them regularly to remove dirt and debris that could be stuck in the seams. It’s also important to communicate with other trades working at the site to ensure that foot traffic and adjacent work aren’t damaging the metal or causing problems with installation.
Installation
After all of the prep work has been done, it’s time for the actual metal roofing installation to begin. It’s important for the contractor to use tools that are compatible with the materials being used in order to create a watertight seal. They should also follow the manufacturer’s instructions to ensure a sturdy, long-lasting roof.
Once the roof deck is clean, a layer of underlayment should be installed over any existing shingles. This will provide a barrier to moisture that could damage the metal panels. It’s also a good idea to install furring strips, which are narrow strips of wood that go horizontally across the roof to level out uneven spots.
It’s important for the contractor to be able to accurately align and fasten the metal panels to the roof. Using a speed square to take angle measurements is an excellent way to ensure that the panels are perfectly straight and level. It’s also a good idea for the contractor to use a chalk line tool to mark straight lines, and to clean the marks afterward. These tools will help to improve the quality of the finished product and will help to keep the project running smoothly.
Then, the panel’s must be trimmed to the desired height and secured to the roof with fasteners. It’s a good idea to use galvanized screws, which are less likely to rust than other types of screws. It’s important that the screws are not over-tightened or under-tightened, as this can lead to leaks. It’s also a good idea the use a bead of sealant around the edges of the panels.
At this point, the roof is ready for a walk-through with the property owner to evaluate the job and make sure everything was done correctly. It’s also a good idea at this time to discuss how payments will be handled, as many contractors accept payment in installments. It’s also a good time to ask about the warranty process, as most contractors will offer a workmanship guarantee for two to five years. This will help to protect the investment and ensure that any problems with the new roof are taken care of quickly.
Finishing
Metal roofs are often the top choice for home and building owners who want a sleek, modern look that can stand up to the unique weather conditions of their region. These unique conditions include extreme temperatures – from well over 100° on summer days to below freezing during winter.
These extreme temperature variations can cause different effects on the metal roofing material. When a home or business owner is researching their options for a new roof, it’s important to understand the differences in these materials so they can make an informed decision about which one will best suit their needs.
Choosing the right metal roofing material will help protect the home or building, increase energy efficiency, and decrease their utility bills. But it’s also important to choose a roofing contractor with experience installing metal roofs, and a track record of excellent customer service. To avoid getting ripped off, a home or business owner should always get a quote from multiple roofing contractors before hiring someone.
A reputable roofing contractor will take the time to discuss the entire project with the home or business owner. This includes discussing the timeline and process, as well as answering questions about what to expect during the installation phase. They should also provide details about the durability and longevity of various metal roof materials to support the customer’s decision-making process.
Once the metal roofing arrives at the job site, it should be stored properly to keep it clean and dry until it’s installed. For example, it’s important to cover the roof if rain is in the forecast. This will prevent any potential damage to the underlayment or other working components.
In addition to protecting the roofing materials, proper storage will also minimize the need for touch-up paint. In some cases, a metal panel’s color may fade over time due to sun exposure or other factors. This is why it’s important to use touch-up paint sparingly.
Finally, the homeowner or business owner should be made aware of any warranty options that come with their metal roof installation. Some manufacturers offer extended warranties, and some even offer maintenance services to ensure that the roof stays in great condition. A reputable contractor will explain the available warranty options, as well as how to apply for them.
Inspection
Metal roofing is a significant investment in your home, and a quality installation is critical to its longevity. A thorough inspection process can identify potential issues and ensure that the job is completed to your satisfaction. The inspection process should include an evaluation of the roof and surrounding areas, a walk around the site with the contractor and a 48-hour window for you to evaluate the work.
Before starting a metal roofing project, the inspector should review the condition of the roof deck to ensure it is strong enough to support the load of a new roof and that it is free of any existing damage or leaks. The inspection should also look at the drainage systems and gutters to ensure they are in good condition.
Next, the inspector should evaluate the underlayment to ensure it is of a high quality and that it will provide adequate moisture resistance for the type of roof being installed. The underlayment should be rolled out in sections starting at the eaves and overlapping each row by 4-6 inches, and it should be sealed along its edges to prevent water infiltration.
Once the underlayment is in place, the contractor can begin installing the panels. It is important that the installers follow the manufacturer’s guidelines when cutting the panels to ensure the fit and longevity of the roof. Panels that are not properly fitted or cut can cause leaks, rust and corrosion, and other issues.
The inspector should also check the flashing and trim to make sure they are properly installed and sealed. This is especially important in areas where the roof meets walls, chimneys, skylights, and other structures. The flashing is designed to create a waterproof barrier in these areas and it is essential that the flashing is correctly installed to prevent water infiltration.
Finally, the inspector should look for any loose screws or misaligned panels and inspect the area around drains, gutters, and downspouts to make sure they are sealed and free of debris. The inspector should also look for any signs of weather-related damage, such as dents or punctures.